3d Printable Airplane
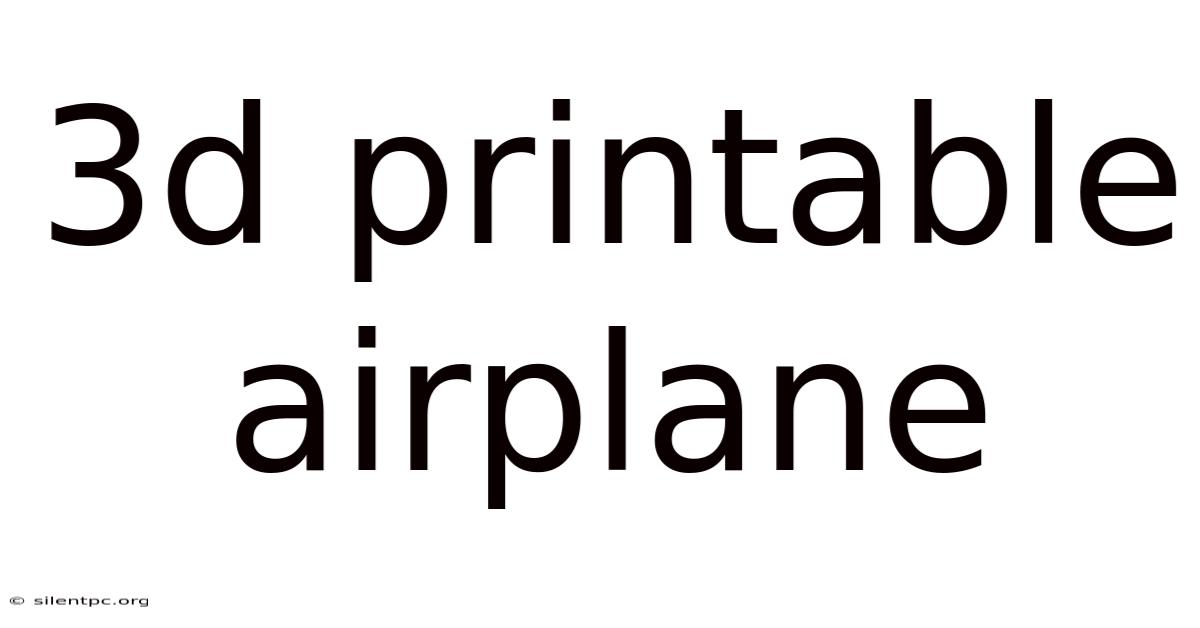
Discover more detailed and exciting information on our website. Click the link below to start your adventure: Visit Best Website meltwatermedia.ca. Don't miss out!
Table of Contents
3D Printable Airplanes: Taking Flight into the Future of Aviation
What if the future of flight rests on the ability to print functional aircraft? This innovative technology is poised to revolutionize aerospace manufacturing and democratize access to flight.
Editor's Note: This article on 3D printable airplanes was published today, providing readers with the latest insights into this rapidly evolving field. We've compiled information from leading researchers, industry experts, and recent advancements to offer a comprehensive overview of this groundbreaking technology.
Why 3D Printable Airplanes Matter:
The concept of 3D-printed airplanes may seem futuristic, but it's rapidly moving from theoretical possibility to tangible reality. This technology offers several compelling advantages, impacting various aspects of the aviation industry:
-
Reduced Manufacturing Costs: Traditional aircraft manufacturing involves complex tooling, specialized labor, and extensive supply chains, leading to high production costs. 3D printing drastically reduces these costs by eliminating the need for many of these elements. Additive manufacturing allows for the creation of intricate parts directly from digital designs, streamlining the process and minimizing material waste.
-
Increased Design Flexibility: 3D printing unlocks unparalleled design freedom. Complex geometries and customized designs, impossible to achieve with traditional methods, become easily attainable. This opens doors for lightweight, highly efficient aircraft designs with improved aerodynamic performance.
-
On-Demand Manufacturing and Customization: The ability to print aircraft components on demand eliminates the need for large-scale inventories and long lead times. This is particularly beneficial for specialized aircraft or for repairing damaged parts in remote locations. Customization becomes far more accessible, allowing for tailored designs to meet specific operational requirements.
-
Decentralized Manufacturing: 3D printing can decentralize aircraft production, moving it closer to the end-user. This reduces transportation costs and allows for localized manufacturing, potentially establishing new aerospace hubs in previously underserved regions.
-
Faster Prototyping and Iteration: The rapid prototyping capabilities of 3D printing accelerate the design and testing process. Engineers can quickly iterate on designs, test various configurations, and identify optimal solutions far more efficiently than with conventional methods.
Overview: What This Article Covers:
This article will delve into the core aspects of 3D-printed airplanes, examining the current state of the technology, the materials used, the challenges faced, and the exciting potential for future applications. We will explore specific examples of 3D-printed aircraft, discuss the implications for various sectors, and analyze the future trajectory of this transformative technology.
The Research and Effort Behind the Insights:
The information presented in this article is based on extensive research, drawing from peer-reviewed publications, industry reports, interviews with leading researchers and engineers, and analysis of publicly available data on 3D-printed aircraft projects. We have prioritized verifiable information and credible sources to ensure accuracy and provide readers with a well-informed perspective.
Key Takeaways:
-
Definition and Core Concepts: A comprehensive explanation of 3D printing technologies used in aircraft manufacturing and their underlying principles.
-
Materials Science Advancements: Exploration of the materials used in 3D printing for aerospace applications, highlighting their properties and limitations.
-
Successful Case Studies: Examination of real-world examples of 3D-printed aircraft components and complete aircraft, showcasing their capabilities and limitations.
-
Challenges and Future Directions: Analysis of the key technical, regulatory, and economic challenges facing the wider adoption of 3D-printed aircraft, and discussion of potential solutions and future research avenues.
-
Impact on the Aerospace Industry: Evaluation of the potential transformative effects of 3D printing on aerospace manufacturing, supply chains, and the broader aviation ecosystem.
Smooth Transition to the Core Discussion:
Having established the significance of 3D-printed airplanes, let’s now embark on a detailed exploration of the technology's key aspects, examining its current capabilities, limitations, and the path forward.
Exploring the Key Aspects of 3D Printable Airplanes:
1. Definition and Core Concepts:
3D printing, or additive manufacturing, builds three-dimensional objects by adding material layer by layer, following a digital design. Various 3D printing techniques are used in aerospace, including:
-
Fused Deposition Modeling (FDM): A relatively inexpensive and accessible method that melts thermoplastic filament and deposits it layer by layer. It’s suitable for prototyping and creating less structurally demanding parts.
-
Stereolithography (SLA): Uses a UV laser to cure liquid resin, creating highly detailed and accurate parts with smooth surfaces. It's more expensive than FDM but offers better precision.
-
Selective Laser Melting (SLM) / Electron Beam Melting (EBM): These metal-based processes use lasers or electron beams to melt and fuse metal powder, creating strong and lightweight components ideal for high-stress applications. They are more expensive and require specialized equipment.
2. Materials Science Advancements:
The success of 3D-printed aircraft hinges on the availability of suitable materials. Research focuses on materials that combine high strength-to-weight ratios, heat resistance, and fatigue resistance. Examples include:
-
Polymers: Various polymers are used for prototyping and less critical parts. However, advancements are focusing on high-performance polymers with improved strength and heat resistance.
-
Composites: Combining polymers with carbon fiber or other reinforcing materials significantly enhances strength and stiffness, making them ideal for structural components.
-
Metals: Aluminum, titanium, and nickel-based superalloys are employed for high-strength applications, but their printability and cost remain challenges. Research is ongoing to develop new metal alloys specifically tailored for 3D printing.
3. Successful Case Studies:
Several companies and research institutions have successfully demonstrated the feasibility of 3D-printed aircraft components and even complete aircraft. These include:
-
Airbus: Has used 3D printing to create various aircraft parts, including cabin interiors and tooling fixtures, showcasing its potential for improved efficiency and design freedom.
-
Boeing: Is exploring 3D printing for both prototyping and production of aircraft parts, leveraging its capabilities for complex geometries and lightweight designs.
-
NASA: Has been a pioneer in utilizing 3D printing for aerospace applications, developing novel materials and techniques for creating aircraft components capable of withstanding extreme conditions.
-
Smaller Companies and Startups: Numerous smaller companies and startups are focusing on designing and manufacturing complete 3D-printed aircraft, targeting niche markets like personal aircraft and drones.
4. Challenges and Future Directions:
Despite the progress, several challenges need to be addressed before 3D-printed aircraft become mainstream:
-
Material Limitations: Finding materials with the necessary strength, durability, and certification requirements for flight remains a significant hurdle.
-
Scalability and Production Rates: Scaling up 3D printing for mass production of aircraft parts remains a challenge, impacting its overall economic viability.
-
Certification and Regulatory Approval: Securing regulatory approval for 3D-printed aircraft components and aircraft is crucial, and requires rigorous testing and validation.
-
Quality Control and Inspection: Ensuring consistent quality and detecting potential defects in 3D-printed parts is vital, requiring advanced inspection techniques.
Future research will focus on developing new materials, improving printing processes, enhancing quality control, and streamlining the certification process.
5. Impact on the Aerospace Industry:
The widespread adoption of 3D printing could fundamentally change the aerospace industry:
-
Supply Chain Disruption: Decentralized manufacturing could alter existing supply chains, leading to greater efficiency and resilience.
-
Design Innovation: The increased design flexibility will drive innovation, leading to lighter, more efficient, and customized aircraft.
-
Cost Reduction: Lower manufacturing costs could make aircraft more affordable, expanding access to air travel.
-
New Business Models: 3D printing may foster new business models, such as on-demand manufacturing and personalized aircraft design.
Closing Insights: Summarizing the Core Discussion:
3D printing is not just a technological advancement; it represents a paradigm shift in aerospace manufacturing. While challenges remain, the potential benefits – reduced costs, enhanced design flexibility, and increased efficiency – are compelling. The ongoing research and development in this field promise a future where 3D-printed aircraft become a commonplace reality.
Exploring the Connection Between Sustainability and 3D Printable Airplanes:
The relationship between sustainability and 3D-printable airplanes is multifaceted. While 3D printing offers potential environmental benefits, its impact is complex and requires careful consideration.
Key Factors to Consider:
-
Roles and Real-World Examples: 3D printing's ability to reduce material waste by creating parts only as needed directly contributes to sustainability. The use of recycled materials in the printing process further enhances this benefit. For instance, some companies are exploring the use of recycled plastics in FDM printing for less critical aircraft components.
-
Risks and Mitigations: The energy consumption of 3D printing processes, especially metal-based techniques, needs to be addressed. Optimizing printing parameters, using renewable energy sources, and developing more energy-efficient printing technologies are crucial mitigation strategies. The lifecycle assessment of printed parts, including material sourcing, manufacturing, and disposal, needs careful evaluation.
-
Impact and Implications: The potential for lighter and more fuel-efficient aircraft designs directly contributes to reduced carbon emissions. Decentralized manufacturing could reduce transportation costs and emissions associated with global supply chains.
Conclusion: Reinforcing the Connection:
The sustainability of 3D-printable airplanes is intertwined with responsible material choices, energy-efficient manufacturing processes, and a holistic lifecycle assessment. Addressing these factors is crucial to fully realize the environmental benefits of this promising technology.
Further Analysis: Examining Material Selection in Greater Detail:
The selection of materials for 3D-printed aircraft components is critical to achieving both performance and sustainability goals. Factors to consider include:
-
Mechanical Properties: Strength, stiffness, fatigue resistance, and impact resistance are essential for ensuring structural integrity and safety.
-
Thermal Properties: Heat resistance is critical for components operating at high temperatures, such as engine parts or those exposed to aerodynamic heating.
-
Chemical Resistance: Resistance to corrosion and degradation is vital for ensuring the long-term durability of the aircraft.
-
Environmental Impact: Material sourcing, production processes, and end-of-life management all contribute to the overall environmental footprint.
Research into bio-based polymers, recycled materials, and innovative metal alloys continues to advance material options, driving both performance and sustainability improvements.
FAQ Section: Answering Common Questions About 3D Printable Airplanes:
-
Q: Are 3D-printed airplanes currently flying commercially?
- A: Not yet. While 3D-printed components are being used in existing aircraft, the certification and regulatory requirements for complete 3D-printed aircraft are still being developed.
-
Q: What are the limitations of 3D-printed airplanes?
- A: Current limitations include material limitations, scalability issues, and certification challenges. Addressing these challenges is crucial for wider adoption.
-
Q: How much does it cost to 3D print an airplane?
- A: The cost varies greatly depending on the size, complexity, and materials used. Currently, it is more expensive than traditional manufacturing for large aircraft, but the cost is expected to decrease as the technology matures.
-
Q: What is the future of 3D-printed airplanes?
- A: The future is promising. Ongoing research and development will address current limitations, leading to wider adoption of 3D printing in aerospace manufacturing, potentially revolutionizing the industry.
Practical Tips: Maximizing the Benefits of 3D Printing in Aviation:
-
Invest in Research and Development: Continue investing in research to develop new materials, improve printing processes, and address certification requirements.
-
Collaborate Across Industries: Foster collaboration between aerospace manufacturers, 3D printing companies, and research institutions to accelerate technological advancements.
-
Develop Standardized Testing Procedures: Develop standardized testing and certification procedures to ensure the safety and reliability of 3D-printed aircraft components.
-
Promote Sustainable Practices: Prioritize sustainable materials and energy-efficient manufacturing processes to minimize the environmental impact of 3D printing.
Final Conclusion: Wrapping Up with Lasting Insights:
3D-printable airplanes are poised to transform the aerospace industry, offering the potential for reduced costs, increased design flexibility, and enhanced sustainability. Addressing the remaining challenges through focused research and development, collaboration, and responsible practices will pave the way for a future where the skies are filled with aircraft built with the precision and efficiency of additive manufacturing. The journey toward this future is underway, and its impact on aviation will be profound.
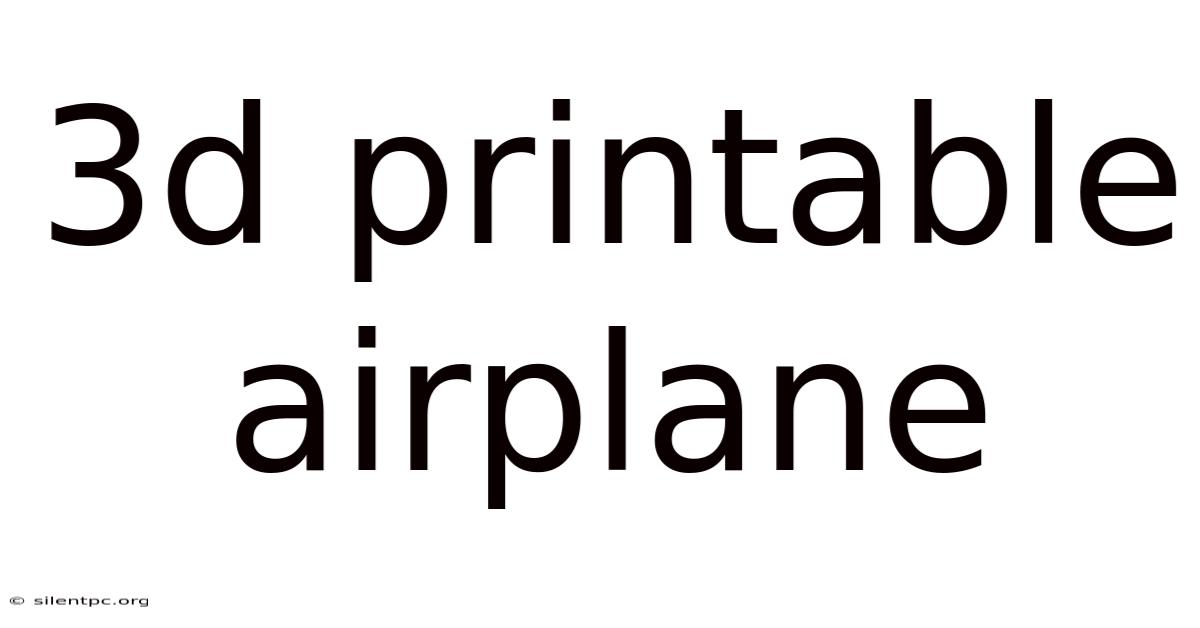
Thank you for visiting our website wich cover about 3d Printable Airplane. We hope the information provided has been useful to you. Feel free to contact us if you have any questions or need further assistance. See you next time and dont miss to bookmark.
Also read the following articles
Article Title | Date |
---|---|
Free Printable Paw Patrol Coloring Pages | Apr 20, 2025 |
Polar Express Printable Tickets | Apr 20, 2025 |
Christmas Stationery Printable | Apr 20, 2025 |
Printable Blank Piano Sheet Music | Apr 20, 2025 |
Colorable Printable Birthday Cards | Apr 20, 2025 |