3d Printable Guitar
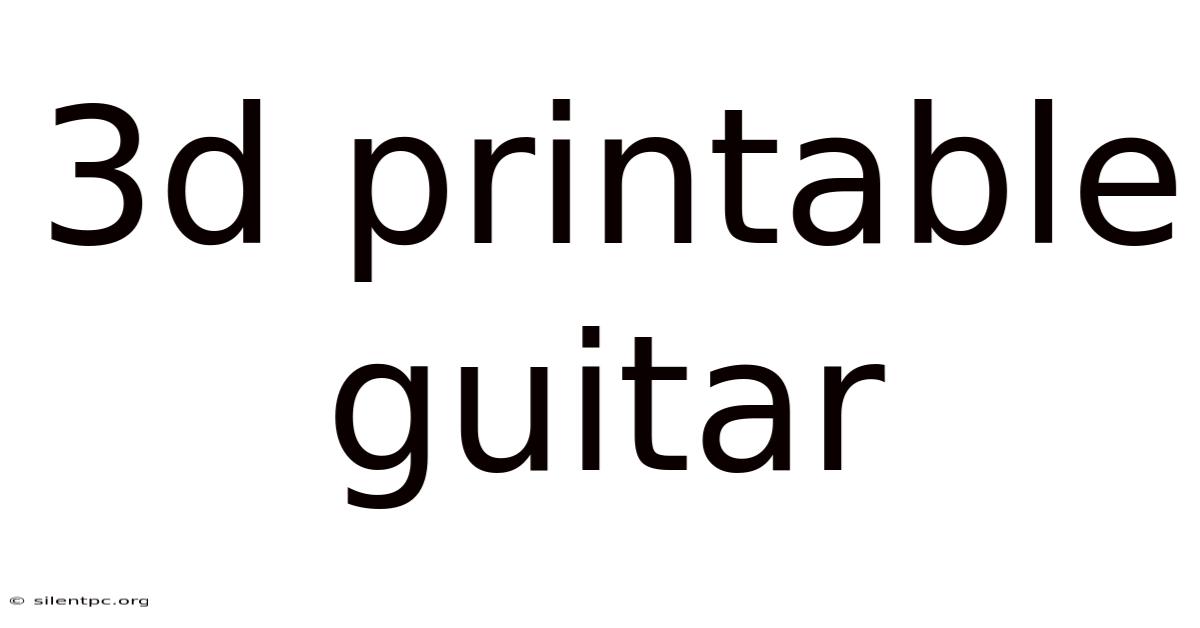
Discover more detailed and exciting information on our website. Click the link below to start your adventure: Visit Best Website meltwatermedia.ca. Don't miss out!
Table of Contents
Unleashing the Six Strings of Innovation: A Deep Dive into 3D Printable Guitars
What if the future of musical instrument creation lies in the intricate layers of 3D-printed plastic? This revolutionary technology is not just reshaping the guitar-making process; it's unlocking a world of customization and design possibilities never before imagined.
Editor’s Note: This article on 3D printable guitars has been published today, offering readers the latest insights into this exciting and rapidly evolving field. We explore the technology, its impact on the industry, and the future implications for musicians and makers alike.
Why 3D Printable Guitars Matter:
The rise of 3D printing is transforming numerous industries, and the world of musical instruments is no exception. 3D printable guitars offer a compelling blend of accessibility, customization, and innovation. For musicians, this means unprecedented control over the design and creation of their instruments, from subtle ergonomic adjustments to radical departures from traditional guitar shapes and materials. For manufacturers, it presents opportunities for streamlined production, reduced material waste, and the ability to cater to niche markets with highly specialized instruments. The implications extend beyond mere aesthetics; 3D printing opens avenues for exploring new sonic properties and enhancing playability through optimized designs. This technology is not just a trend; it’s a catalyst for the future of guitar making.
Overview: What This Article Covers:
This article provides a comprehensive exploration of 3D printable guitars. We’ll delve into the technology behind the process, examine the advantages and disadvantages, discuss design considerations, explore the diverse applications within the industry, and analyze the challenges and future possibilities. Readers will gain a thorough understanding of this innovative approach to instrument creation and its implications for musicians, manufacturers, and the future of music.
The Research and Effort Behind the Insights:
This article is the result of extensive research, incorporating information from academic publications, industry reports, interviews with 3D printing guitar builders, and analysis of commercially available 3D-printed guitar designs. We've meticulously examined the technical specifications, design principles, and market trends to provide readers with accurate, up-to-date, and insightful information.
Key Takeaways:
- Definition and Core Concepts: A clear understanding of 3D printing technologies and their application in guitar construction.
- Practical Applications: Exploration of various 3D-printed guitar designs, materials, and their sonic characteristics.
- Challenges and Solutions: Analysis of the limitations of 3D printing for guitars and potential solutions to overcome them.
- Future Implications: A look at the potential future developments and impact of this technology on the music industry.
Smooth Transition to the Core Discussion:
Now that we've established the significance of 3D printable guitars, let's explore the specifics of this innovative approach to instrument making.
Exploring the Key Aspects of 3D Printable Guitars:
1. Definition and Core Concepts:
3D printing, also known as additive manufacturing, builds three-dimensional objects layer by layer from a digital design. Several techniques are used, including Fused Deposition Modeling (FDM), Stereolithography (SLA), and Selective Laser Sintering (SLS). Each method has its strengths and weaknesses concerning material properties, detail resolution, and build speed, all crucial considerations when designing a 3D-printable guitar. FDM is often chosen for its accessibility and lower cost, while SLA and SLS offer greater precision and stronger, more durable end products. The choice of technology heavily influences the final guitar's quality, durability, and overall sound.
2. Applications Across Industries:
The applications of 3D-printed guitars extend beyond individual hobbyists and small-scale manufacturers. Larger companies are starting to explore 3D printing for prototyping, creating custom instruments for high-profile artists, or producing limited-edition runs. The ability to rapidly prototype new designs and test different materials without extensive tooling costs makes 3D printing a powerful tool for research and development in the musical instrument industry. This also allows for greater customization of guitars for players with specific physical needs or preferences.
3. Challenges and Solutions:
While 3D printing offers numerous advantages, it also presents challenges. One key limitation is the strength and durability of the printed materials compared to traditional wood or composite materials. Certain plastics may not withstand the stress of regular playing, especially for instruments subjected to vigorous use. This is mitigated by exploring stronger polymers, incorporating internal reinforcements, or using hybrid designs that combine 3D-printed components with traditional materials like wood for the neck and fretboard. Another challenge is achieving the desirable acoustic properties. 3D-printed guitars may require careful design and material selection to achieve the resonance and tonal qualities expected in a traditional instrument. The ongoing development of new materials and printing techniques is steadily addressing these challenges.
4. Impact on Innovation:
3D printing empowers a new generation of guitar makers and designers, fostering creativity and experimentation. The technology allows for the creation of complex and intricate designs that would be impossible or prohibitively expensive with traditional manufacturing methods. It has also led to the exploration of entirely new guitar shapes and ergonomic designs, potentially improving playability and comfort for musicians. The ability to customize guitars to individual specifications opens doors for personalized instruments tailored to the musician's unique needs and preferences.
Closing Insights: Summarizing the Core Discussion:
3D-printed guitars represent a paradigm shift in instrument creation. The technology's accessibility, customization potential, and rapid prototyping capabilities are transforming the way guitars are designed, manufactured, and experienced. While challenges remain, the ongoing development of materials and printing techniques continually improves the quality, durability, and sonic capabilities of 3D-printed guitars, solidifying their place in the future of music.
Exploring the Connection Between Material Selection and 3D Printable Guitars:
The choice of material is paramount in 3D printing guitars. The properties of the filament directly impact the instrument's sound, durability, and overall playability.
Roles and Real-World Examples:
ABS (Acrylonitrile Butadiene Styrene) is a popular choice due to its strength and relatively low cost. Many early 3D-printed guitars utilized ABS, demonstrating its feasibility, although its acoustic properties aren't ideal. PLA (Polylactic Acid) is a biodegradable and environmentally friendly option, but it’s generally less durable than ABS. However, advancements in PLA formulations are making it a more viable option for certain guitar components. More recently, high-performance polymers like Nylon and PETG are being explored, offering enhanced strength, resilience, and potentially improved acoustic characteristics. Companies are experimenting with composite materials, embedding conductive filaments to create unique electronic functionalities within the instrument's body.
Risks and Mitigations:
Using less durable filaments can result in cracked or broken parts, especially in areas subjected to high stress like the bridge or headstock. This is mitigated by careful design, reinforcing critical areas, or using hybrid designs that incorporate traditional materials. The material's inherent acoustic properties also need to be carefully considered. Some materials may dampen the sound excessively, requiring compensatory design changes to ensure proper resonance.
Impact and Implications:
The material selection significantly influences the guitar's final sound and longevity. The use of stronger, more acoustically resonant materials will lead to improved instruments, potentially closing the sonic gap between traditional and 3D-printed guitars. The exploration of new and innovative materials will continuously expand the design possibilities and further drive innovation in 3D-printed instrument creation.
Conclusion: Reinforcing the Connection:
The material's properties are inextricably linked to the success of 3D-printed guitars. Choosing the right material, considering its strengths and limitations, and incorporating innovative design solutions are crucial for realizing the full potential of this technology.
Further Analysis: Examining Material Properties in Greater Detail:
Each 3D printing filament possesses unique mechanical and acoustic properties. ABS, for instance, offers high impact resistance but can be brittle, requiring careful design to prevent cracking. PLA is relatively easy to print, but its lower strength necessitates strategic reinforcement in stress-bearing areas. Nylon offers excellent flexibility and durability, making it a suitable option for parts that require bending or flexing. The ongoing research into new materials with improved acoustic properties and enhanced durability is essential for the continued evolution of 3D-printed guitars. This involves analyzing the material's density, stiffness, and resonance characteristics to predict its behavior and optimize the design for optimal acoustic performance.
FAQ Section: Answering Common Questions About 3D Printable Guitars:
Q: Are 3D-printed guitars durable enough for regular playing?
A: The durability depends on the material and design. High-performance polymers and strategic reinforcements can create guitars that withstand regular use. However, some 3D-printed guitars might be better suited for lighter playing styles or studio use.
Q: How do 3D-printed guitars sound compared to traditional guitars?
A: The sound can vary greatly depending on the material, design, and printing process. Some 3D-printed guitars can achieve a surprisingly good tone, while others might have a less resonant or brighter sound than traditional instruments. Ongoing development aims to bridge this sonic gap.
Q: How much does a 3D-printed guitar cost?
A: The cost can range significantly depending on the material, complexity of the design, and the printing service used. Some simpler designs can be relatively inexpensive, while more complex models can be quite costly.
Q: Can I 3D print a guitar myself?
A: Yes, but it requires access to a 3D printer, the necessary software, and a well-designed digital model. It's a challenging project, and experience with 3D printing is highly recommended.
Practical Tips: Maximizing the Benefits of 3D Printable Guitars:
- Understand the Basics: Research different 3D printing technologies, materials, and design considerations before starting a project.
- Choose the Right Material: Select a material that balances strength, durability, and acoustic properties based on your intended use.
- Design for Strength: Reinforce stress points in your design to prevent cracking or breakage.
- Consider Hybrid Designs: Combine 3D-printed parts with traditional materials like wood for the best results.
- Experiment and Iterate: Don't be afraid to experiment with different designs and materials. Iteration is key to optimizing your 3D-printed guitar.
Final Conclusion: Wrapping Up with Lasting Insights:
3D-printed guitars represent a significant advancement in instrument making. While challenges remain, the technology's potential to revolutionize the guitar industry is undeniable. The ability to customize designs, rapidly prototype new ideas, and explore innovative materials is unlocking unprecedented creative possibilities. As 3D printing technology and materials continue to evolve, the future of 3D-printed guitars is bright, promising a new era of musical innovation and accessibility.
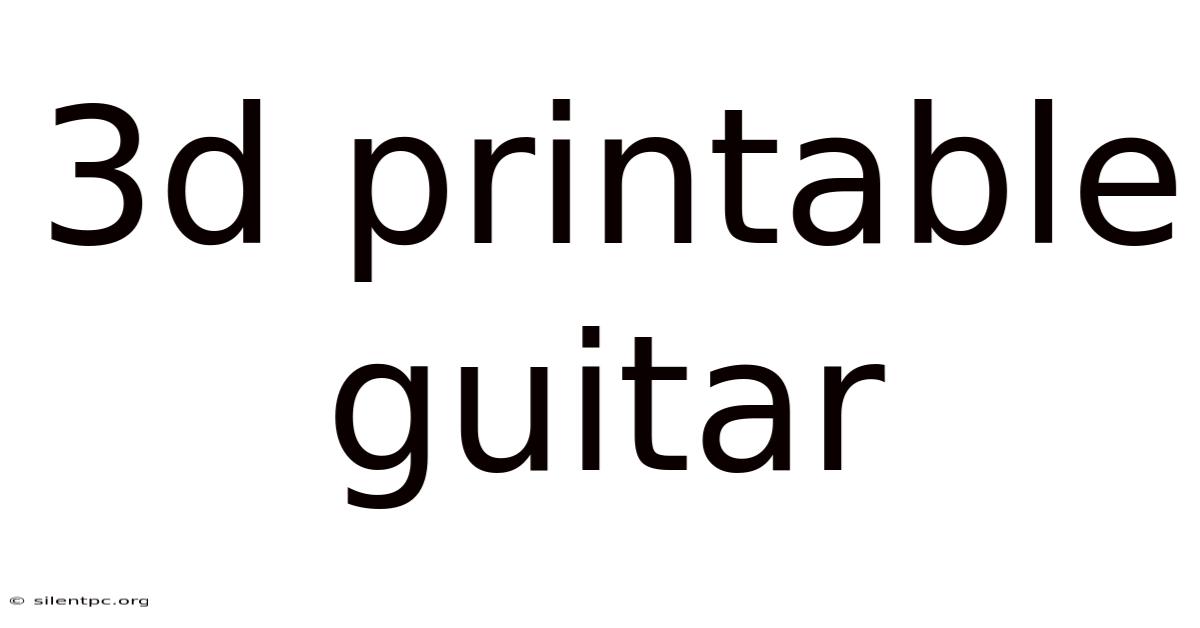
Thank you for visiting our website wich cover about 3d Printable Guitar. We hope the information provided has been useful to you. Feel free to contact us if you have any questions or need further assistance. See you next time and dont miss to bookmark.
Also read the following articles
Article Title | Date |
---|---|
Word Search Template Printable | Apr 10, 2025 |
Adult Dot To Dot Printables | Apr 10, 2025 |
3 Inch Printable Letter Stencils | Apr 10, 2025 |
Alphabet Block Letters Printable | Apr 10, 2025 |
Wacky Wednesday Printables | Apr 10, 2025 |