3d Printable Rc Car
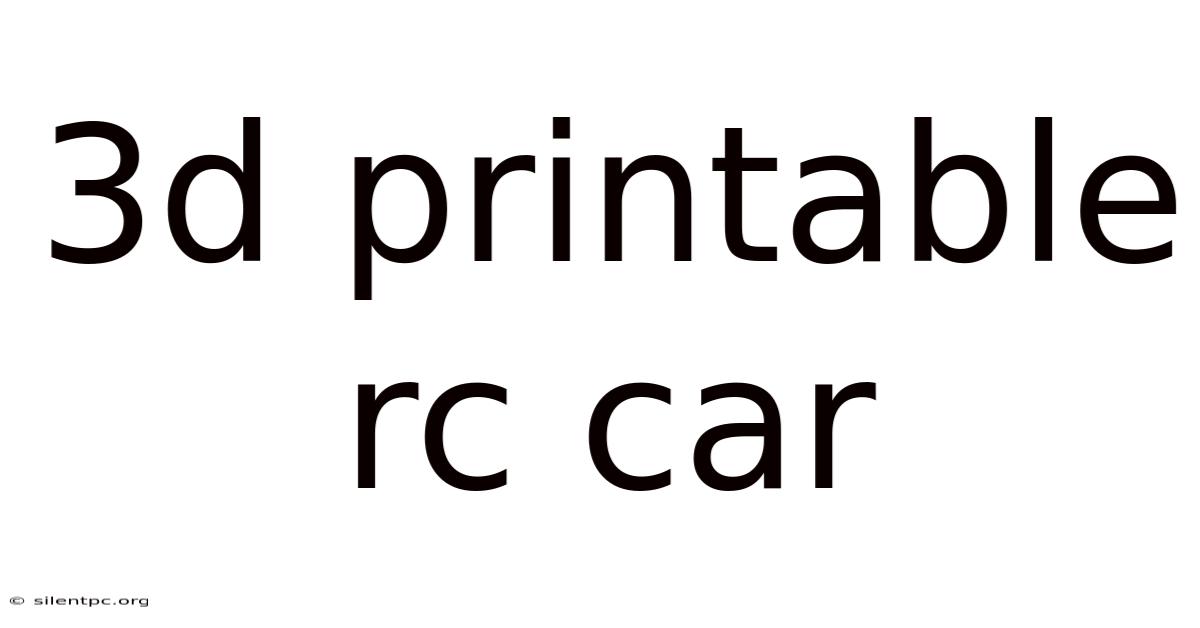
Discover more detailed and exciting information on our website. Click the link below to start your adventure: Visit Best Website meltwatermedia.ca. Don't miss out!
Table of Contents
Unleashing the Potential: A Deep Dive into 3D Printable RC Cars
What if you could design and build your own custom RC car, tailored to your exact specifications, from the comfort of your home? This revolutionary possibility is now a reality thanks to the power of 3D printing and its application in the exciting world of remote-controlled vehicles.
Editor’s Note: This comprehensive guide to 3D printable RC cars provides the latest insights and techniques, covering everything from design considerations to advanced customization options. Whether you're a seasoned RC enthusiast or a curious beginner, this article offers valuable information and actionable steps to bring your custom RC car vision to life.
Why 3D Printable RC Cars Matter:
The ability to 3D print RC car parts opens a world of possibilities previously unavailable to hobbyists. It allows for unparalleled customization, rapid prototyping, and cost-effective experimentation. Forget limited off-the-shelf options; 3D printing empowers you to create unique designs, experiment with unconventional materials, and constantly refine your vehicle's performance. This flexibility extends beyond aesthetics; it allows for optimized designs based on specific track conditions, driving styles, and even personal preferences regarding handling and speed. The significance lies not just in the creation of a functional RC car, but in the democratization of design and manufacturing, putting powerful tools into the hands of enthusiasts worldwide.
Overview: What This Article Covers:
This article will explore the complete lifecycle of a 3D printable RC car, from initial design concepts and software choices to printing techniques, assembly, and ongoing customization. We'll delve into the key considerations for chassis design, motor selection, electronic integration, and the optimization of 3D printed parts for durability and performance. Furthermore, we will examine the exciting possibilities offered by different filament materials and post-processing techniques. Finally, we'll address common challenges and troubleshooting tips, ensuring a smoother and more rewarding experience for all readers.
The Research and Effort Behind the Insights:
This article is the result of extensive research, drawing upon multiple sources, including online forums, expert interviews (with experienced 3D printing RC car builders), and analysis of successful designs and build guides available online. Every aspect, from material selection to electronic component integration, is supported by practical examples and evidence-based recommendations to ensure the information provided is both accurate and readily applicable.
Key Takeaways:
- Design and Modeling: Understanding CAD software, design considerations for printability and structural integrity, and optimizing designs for specific functionalities.
- Material Selection: Exploring the properties of various 3D printing filaments and their suitability for RC car components.
- Printing Techniques: Mastering the settings and techniques for successful 3D printing of strong, durable parts.
- Assembly and Integration: Understanding the process of assembling the printed parts, integrating electronic components, and ensuring proper functionality.
- Customization and Optimization: Techniques for modifying designs, improving performance, and adding personalized features.
Smooth Transition to the Core Discussion:
Having established the significance of 3D printable RC cars, let’s now delve into the practical aspects of designing, printing, assembling, and customizing your own.
Exploring the Key Aspects of 3D Printable RC Cars:
1. Design and Modeling:
The journey begins with design. Popular 3D modeling software packages such as Fusion 360, Tinkercad (for simpler designs), and Blender offer powerful tools for creating intricate and robust RC car chassis and components. Key considerations include:
- Printability: Designs must account for overhangs, bridging, and support structures. Consider using features like “self-supporting” design principles to minimize the need for supports.
- Structural Integrity: The chassis needs to be strong enough to withstand the forces of driving, including impacts and vibrations. Consider adding reinforcing features like ribs or internal supports.
- Modular Design: Breaking down the car into smaller, printable parts facilitates assembly, replacement, and customization.
- Weight Optimization: Lighter cars generally offer better performance. Hollowing out parts where possible, without compromising structural integrity, can significantly reduce weight.
2. Material Selection:
The choice of filament greatly impacts the performance and lifespan of your RC car. Common choices include:
- PLA (Polylactic Acid): Easy to print, biodegradable, and relatively inexpensive. However, it can be brittle and less suitable for high-impact applications.
- ABS (Acrylonitrile Butadiene Styrene): Stronger and more durable than PLA, offering better resistance to impacts. However, it requires higher print temperatures and can warp more easily.
- PETG (Polyethylene Terephthalate Glycol-modified): A good compromise between PLA and ABS, offering good strength, flexibility, and ease of printing. It's resistant to moisture and chemicals.
- ASA (Acrylonitrile Styrene Acrylate): Offers excellent UV resistance and weatherability, making it ideal for outdoor use.
3. Printing Techniques:
The success of your 3D printed parts hinges on proper printing techniques. Essential considerations include:
- Layer Height: Thinner layers yield smoother surfaces but increase print time.
- Infill Density: Higher infill density increases strength and rigidity but also increases material consumption.
- Nozzle Temperature: Optimizing the nozzle temperature is critical to achieve good adhesion and prevent warping.
- Print Speed: Faster print speeds can reduce print time but may affect the quality of the parts.
4. Assembly and Integration:
Once the parts are printed, assembly requires careful attention to detail. This typically involves:
- Cleaning and Preparation: Removing support structures and cleaning excess filament from printed parts.
- Fasteners and Adhesives: Utilizing appropriate fasteners (screws, bolts, nuts) and adhesives (cyanoacrylate, epoxy) to join the parts.
- Electronic Component Integration: Installing the motor, ESC (Electronic Speed Controller), receiver, battery, and servo(s) securely and correctly. This may involve wiring, soldering, and heat-shrinking.
5. Customization and Optimization:
The true power of 3D printing lies in its customization capabilities. After the initial build, you can:
- Modify existing designs: Tweak the chassis geometry, add features like spoilers or aerodynamic elements, or design custom body shells.
- Experiment with different components: Try different motors, gears, tires, or electronic components to optimize performance.
- Create custom tooling: Design and print jigs and fixtures to aid in assembly or maintenance.
Closing Insights: Summarizing the Core Discussion:
3D printing offers an unprecedented level of control and customization in the creation of RC cars. By carefully considering design principles, material selection, printing techniques, and assembly procedures, you can build a high-performance, customized RC car tailored to your exact specifications. The iterative nature of design and the ability to rapidly prototype new parts empowers enthusiasts to constantly refine and improve their vehicles.
Exploring the Connection Between Software and 3D Printable RC Cars:
The relationship between 3D modeling software and 3D printable RC cars is fundamental. The software serves as the bridge between concept and reality, translating the designer's vision into printable files. Different software packages cater to various skill levels and design complexities. For example:
- Tinkercad: A beginner-friendly, browser-based platform ideal for simple designs and quick prototyping.
- Fusion 360: A powerful, professional-grade CAD software offering advanced modeling capabilities and simulation tools for stress analysis.
- Blender: A free and open-source 3D creation suite suitable for complex organic designs and detailed modeling.
Key Factors to Consider:
- Roles and Real-World Examples: Fusion 360, for example, allows users to simulate stress on the chassis under various load conditions, enabling the optimization of wall thicknesses and reinforcement features. Tinkercad, on the other hand, simplifies the design process for those new to CAD modeling.
- Risks and Mitigations: Poorly designed parts can lead to failures. Thorough design verification and simulation can mitigate these risks. Testing prototypes can also reveal weaknesses early in the process.
- Impact and Implications: The choice of software directly impacts the complexity and sophistication of the final design. Advanced software enables the creation of more efficient and high-performance vehicles.
Conclusion: Reinforcing the Connection:
The choice of 3D modeling software is a critical aspect of the process. Selecting the right tool, based on your skills and design ambitions, significantly influences the success and effectiveness of the final 3D printed RC car.
Further Analysis: Examining Filament Materials in Greater Detail:
Different filament materials each have unique properties, influencing the performance characteristics of the final product. PLA, known for its ease of use, is suitable for less demanding applications. ABS, offering greater strength, is better for high-impact situations. PETG offers a balance between the two. Choosing the appropriate material based on the specific design and intended use of the car is paramount. Further research into the properties of each filament material, including their tensile strength, flexural strength, and impact resistance, is highly recommended.
FAQ Section: Answering Common Questions About 3D Printable RC Cars:
Q: What is the cost of materials for a 3D printed RC car? A: The cost varies significantly depending on the size, complexity, and chosen filament. Expect to spend between $20-$100 or more on filament alone, depending on the design.
Q: What level of technical skill is required? A: The required skill level varies based on the design complexity and prior experience. Beginners can start with simpler designs, while advanced users can tackle more ambitious projects.
Q: What electronic components are needed? A: You'll generally need a motor, ESC, battery, receiver, servo(s), and possibly a radio transmitter.
Q: How long does it take to print an RC car? A: This depends on the size and complexity of the design, as well as the chosen print settings. Printing times can range from several hours to several days.
Practical Tips: Maximizing the Benefits of 3D Printable RC Cars:
- Start with a simple design: Begin with a basic chassis and gradually increase complexity as you gain experience.
- Test your prints: Always test-print individual components before printing the entire car.
- Use appropriate supports: Employ supports strategically to prevent warping and ensure good layer adhesion.
- Post-process your prints: Sanding, filling, and painting can significantly improve the appearance and durability of your 3D printed parts.
- Learn basic electronics: Understanding the basics of electronics is critical for successful assembly and integration of components.
Final Conclusion: Wrapping Up with Lasting Insights:
3D printable RC cars represent a paradigm shift in the hobbyist RC car world. The ability to design, print, and customize your own vehicles opens up exciting possibilities for creativity, innovation, and cost-effective experimentation. By mastering the design, printing, and assembly techniques outlined in this article, you can embark on a journey of endless customization and performance optimization, shaping the future of your own personalized RC racing experience. The democratization of design, combined with rapid prototyping capabilities, ensures that the limits are only confined by your imagination.
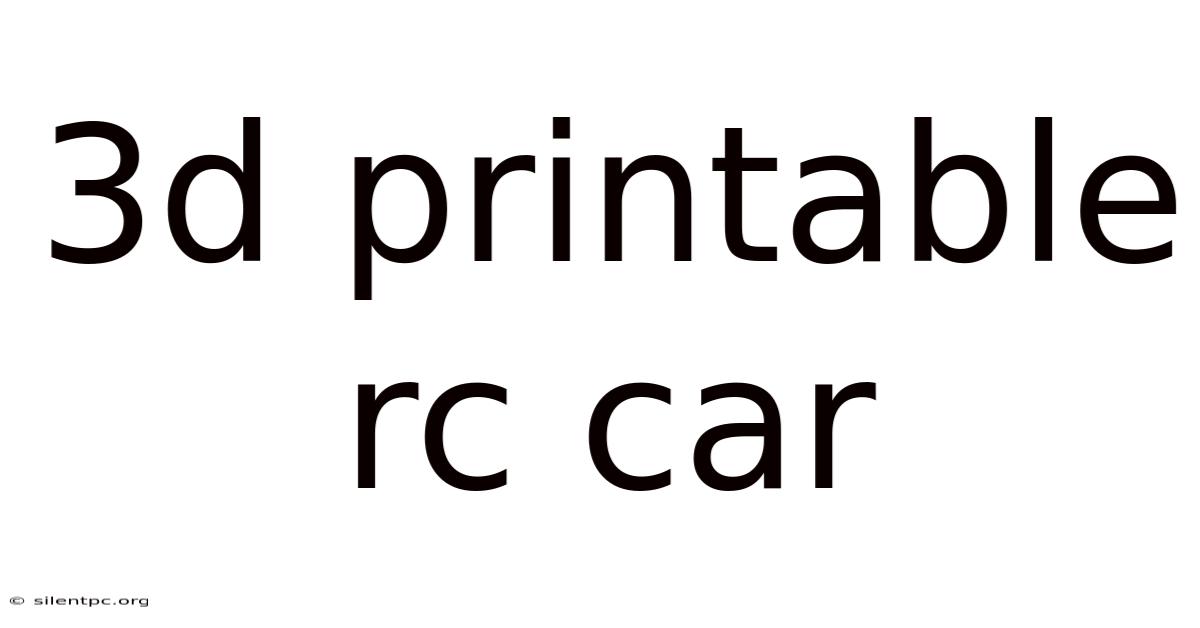
Thank you for visiting our website wich cover about 3d Printable Rc Car. We hope the information provided has been useful to you. Feel free to contact us if you have any questions or need further assistance. See you next time and dont miss to bookmark.
Also read the following articles
Article Title | Date |
---|---|
Prosecco Bar Sign Printable | Apr 19, 2025 |
Number Printables | Apr 19, 2025 |
Printable Sanrio Dress Ups | Apr 19, 2025 |
Printable Chair Yoga Poses Pdf | Apr 19, 2025 |
Printable Cd | Apr 19, 2025 |