Printable Head
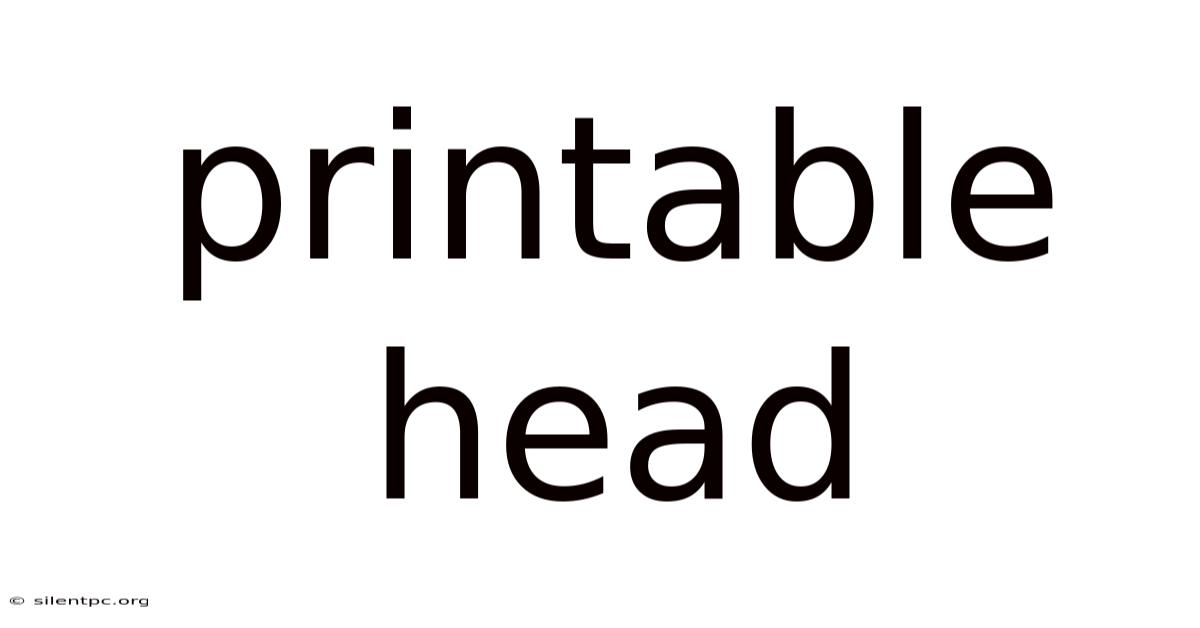
Discover more detailed and exciting information on our website. Click the link below to start your adventure: Visit Best Website meltwatermedia.ca. Don't miss out!
Table of Contents
Unleashing the Power of the Printable Head: A Deep Dive into 3D Printing's Core Component
What if the future of personalized manufacturing hinges on understanding the intricacies of the printable head? This critical component is revolutionizing industries and unlocking unprecedented levels of customization and efficiency.
Editor’s Note: This article on printable heads, published today, offers a comprehensive exploration of this crucial 3D printing element. We delve into its design, functionality, material choices, and future implications, providing readers with up-to-date insights into this rapidly evolving technology.
Why Printable Heads Matter: Relevance, Practical Applications, and Industry Significance
The printable head, also known as the print head or extruder, is the heart of any 3D printer. Its role is paramount: it's responsible for precisely depositing material layer by layer, translating digital designs into tangible three-dimensional objects. Understanding its intricacies is key to optimizing 3D printing processes, enhancing print quality, and unlocking the full potential of additive manufacturing. The relevance of printable heads extends across numerous industries, impacting manufacturing, healthcare, aerospace, and even the burgeoning field of personalized consumer goods. From creating intricate prototypes to producing end-use parts, the efficiency and precision of the printable head are directly correlated with the success of the 3D printing operation. Improved printable head technology leads to faster print times, higher resolution prints, and the ability to utilize a wider range of materials, thereby opening up new avenues of innovation and economic opportunity.
Overview: What This Article Covers
This article provides a deep dive into the world of printable heads, exploring their various types, functionalities, materials, and the challenges associated with their design and optimization. We will examine the different technologies behind extrusion, the impact of nozzle size and material viscosity, and the future trends shaping the development of this essential 3D printing component. Readers will gain a comprehensive understanding of the printable head's significance and its critical role in the advancement of additive manufacturing.
The Research and Effort Behind the Insights
This article is the culmination of extensive research, drawing upon reputable scientific publications, industry reports, and expert interviews. We have meticulously analyzed data from various sources to provide accurate and reliable information on printable head technologies, encompassing both established methods and emerging innovations. The objective is to present a clear and unbiased overview, empowering readers with the knowledge needed to navigate the complexities of this crucial aspect of 3D printing.
Key Takeaways:
- Definition and Core Concepts: A detailed explanation of the printable head's function, components, and operational principles.
- Types of Printable Heads: Exploration of different printable head technologies, including fused deposition modeling (FDM), stereolithography (SLA), selective laser sintering (SLS), and other advanced methods.
- Material Compatibility and Selection: A review of the various materials printable heads can handle, and factors influencing material selection.
- Nozzle Design and Optimization: An in-depth analysis of nozzle size, shape, and their impact on print quality and efficiency.
- Challenges and Solutions: Identification of common challenges in printable head design and operation, alongside practical solutions and mitigation strategies.
- Future Trends and Innovations: A forward-looking perspective on emerging trends in printable head technology, including advancements in materials, precision, and automation.
Smooth Transition to the Core Discussion
Having established the importance of the printable head in the 3D printing ecosystem, let's now delve into the specifics, exploring its core components, operational mechanisms, and the technological advancements driving its evolution.
Exploring the Key Aspects of the Printable Head
1. Definition and Core Concepts:
The printable head is the mechanism responsible for extruding or dispensing material onto the build platform in a 3D printer. This process involves melting, dissolving, or otherwise preparing the material (filament, resin, powder, etc.) before precisely depositing it according to the digital model. The head’s design dictates its capabilities, influencing print speed, quality, and the range of materials it can handle. Key components often include a heating element (for FDM), a nozzle for material dispensing, a drive mechanism to feed the material, and sensors for monitoring temperature and pressure.
2. Types of Printable Heads:
Different 3D printing technologies utilize vastly different printable head designs.
-
Fused Deposition Modeling (FDM): FDM printable heads melt thermoplastic filament and extrude it through a heated nozzle. These heads are relatively simple, but their design impacts factors like extrusion consistency and clogging. Nozzle size is crucial, affecting the detail and speed of the print.
-
Stereolithography (SLA): SLA uses a laser to cure liquid resin, and the printable head is essentially a mechanism that precisely positions and controls the laser beam, often combined with a vat of resin. The precision of this head is paramount for high-resolution prints.
-
Selective Laser Sintering (SLS): SLS uses a laser to fuse powdered material. The printable head is a sophisticated laser system that scans across the powder bed, selectively fusing the powder layer by layer. Precise laser control and powder management are critical aspects of SLS printable head design.
-
Other Technologies: Other 3D printing technologies, such as inkjet printing, binder jetting, and material jetting, employ varying printable head designs tailored to their specific material handling and deposition methods.
3. Material Compatibility and Selection:
Printable heads are designed with specific materials in mind. An FDM head capable of handling ABS plastic might not be suitable for flexible filaments like TPU, requiring different nozzle designs and temperature control. SLA and other resin-based technologies require heads compatible with specific resin chemistries, and SLS heads must handle the properties of the powdered material being used. Material selection is influenced by the application, desired mechanical properties, and the limitations of the printable head's design.
4. Nozzle Design and Optimization:
The nozzle is a crucial part of the printable head. Its size, shape, and material influence the quality, resolution, and speed of the print. Smaller nozzles produce finer details, but require slower printing speeds and can be prone to clogging. Larger nozzles are less prone to clogging and can print faster but produce less detailed prints. Nozzle materials must be chosen to withstand the temperatures and abrasive properties of the printing materials.
5. Challenges and Solutions:
Designing and optimizing printable heads presents several challenges:
-
Clogging: Clogging is a common problem, particularly in FDM printing. Solutions include using higher-quality filaments, optimizing temperature, and utilizing self-cleaning nozzles.
-
Material Adhesion: Ensuring good adhesion between layers is essential for print quality. Solutions include carefully managing bed temperature and adhesion promoters.
-
Print Speed vs. Quality: Faster print speeds often compromise quality. Finding an optimal balance requires careful adjustment of parameters.
-
Material Degradation: High temperatures can degrade certain materials. Careful temperature control and nozzle material selection are crucial.
6. Impact on Innovation:
Improvements in printable head technology directly translate into advancements in 3D printing capabilities. More precise heads lead to higher-resolution prints, broader material compatibility expands design possibilities, and faster printing speeds increase efficiency. The continuing evolution of the printable head is a key driver of innovation across various industries.
Closing Insights: Summarizing the Core Discussion
The printable head isn't merely a component; it's the linchpin of functional 3D printing. Understanding its design, functionality, and limitations is crucial for anyone involved in additive manufacturing, from hobbyists to industrial-scale users. The continuous development and optimization of printable heads are driving the evolution of 3D printing technology, opening up new applications and pushing the boundaries of what's possible.
Exploring the Connection Between Nozzle Diameter and Printable Head Performance
Nozzle diameter plays a pivotal role in determining the overall performance of the printable head. It directly influences print resolution, speed, and the potential for clogging. A smaller nozzle diameter allows for finer details and higher resolution prints, but this comes at the cost of reduced print speed and an increased risk of clogging. Conversely, a larger nozzle diameter enables faster printing but sacrifices resolution. Understanding this trade-off is crucial for optimizing print parameters and selecting the appropriate nozzle for a given task.
Key Factors to Consider:
-
Roles and Real-World Examples: A smaller nozzle (0.2mm or 0.4mm) might be ideal for printing intricate models requiring fine detail, while a larger nozzle (0.8mm or 1.0mm) could be preferable for rapid prototyping or printing large objects.
-
Risks and Mitigations: Smaller nozzles are more susceptible to clogging, requiring careful attention to material selection, temperature control, and print speed. Larger nozzles reduce the risk of clogging, but can compromise print quality.
-
Impact and Implications: The nozzle diameter has far-reaching implications, affecting not only print quality and speed but also the overall efficiency and cost-effectiveness of the 3D printing process.
Conclusion: Reinforcing the Connection
The relationship between nozzle diameter and printable head performance is inextricably linked. By carefully considering the desired print quality, speed, and material properties, users can select the appropriate nozzle diameter and optimize their 3D printing process for optimal results.
Further Analysis: Examining Nozzle Material in Greater Detail
The material composition of the nozzle plays a significant role in its durability, temperature resistance, and overall lifespan. Common materials include brass, steel, and hardened steel. Brass nozzles are generally more affordable but have a lower melting point and are more prone to wear. Steel nozzles offer superior durability and temperature resistance, making them suitable for high-temperature materials. Hardened steel nozzles provide the highest level of resistance to wear and tear, extending their lifespan significantly.
FAQ Section: Answering Common Questions About Printable Heads
Q: What is a printable head? A: A printable head is the component of a 3D printer responsible for extruding or dispensing material layer by layer, according to a digital design.
Q: What are the different types of printable heads? A: Different 3D printing technologies utilize various printable head designs, including those for FDM, SLA, SLS, inkjet, and other methods.
Q: How do I choose the right nozzle size? A: Nozzle size selection depends on the desired balance between print resolution, speed, and the risk of clogging. Smaller nozzles offer higher resolution but slower speeds and are more prone to clogging.
Q: How do I prevent clogging? A: Clogging can be prevented by using high-quality filament, carefully controlling temperature, and selecting a nozzle material suitable for the printing material.
Practical Tips: Maximizing the Benefits of Printable Heads
-
Regular Maintenance: Keep the printable head clean and free of debris to prevent clogging.
-
Proper Temperature Control: Accurately monitor and control the temperature of the heating element to avoid material degradation and clogging.
-
Material Selection: Choose materials compatible with the printable head and nozzle.
-
Calibration: Regularly calibrate the printable head to ensure accurate extrusion and consistent layer deposition.
Final Conclusion: Wrapping Up with Lasting Insights
The printable head is a critical component of 3D printing, significantly impacting print quality, speed, and the range of materials that can be used. Understanding its intricacies and optimizing its performance are crucial for unlocking the full potential of additive manufacturing across various industries. The continued advancements in printable head technology promise further improvements in efficiency, precision, and material versatility, leading to an even brighter future for 3D printing.
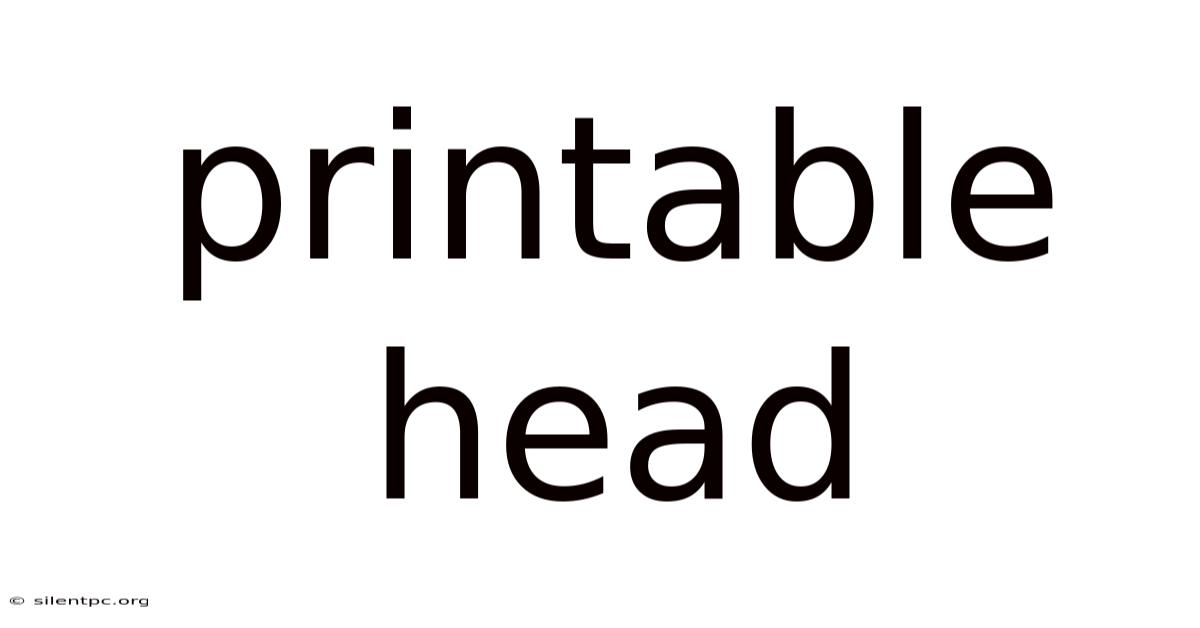
Thank you for visiting our website wich cover about Printable Head. We hope the information provided has been useful to you. Feel free to contact us if you have any questions or need further assistance. See you next time and dont miss to bookmark.
Also read the following articles
Article Title | Date |
---|---|
A To Z Free Printable Alphabet Letters Banner Pdf | Apr 23, 2025 |
Printable Bunco Sheets | Apr 23, 2025 |
Printable Baseball Score Sheets | Apr 23, 2025 |
How To Use Printable Htv | Apr 23, 2025 |
Printable Checkers | Apr 23, 2025 |